Gorilla Glass:
Jason Pfohl Interview
“If it's safe to store tequila in, it's safe to wear in your ears.”
Alright, I admit I'm misquoting Jason a bit... Let's be a bit more professional...
“Glass making is a skill and an art form — it is not injected molded or machined jewelry.”
Both statements are true — glass is a great material, with amazing inherent biocompatibility, and a nature that forces one to work it by hand for the best results. Glass products both compete with the best modern body jewelry with ASTM-spec materials, yet still maintain the marks of jewelry crafted by an artisan rather than a machine. Mexico-based Gorilla Glass (GetGorilla.com, available at BMEshop), run by ex-pat Jason Pfohl (iam:gorilla) in Oaxaca, is an excellent example of a company that does just that.
Ryan Warden (iam:badseeds) of BMEshop recently chatted with Jason about how he went from hippie kid, to a glass fashion artist featured in Vogue, to his current life making some of the world's nicest body jewelry in Oaxaca, Mexico.
***
So give me a brief history of Jason....
I was born in the seventies with hippie parents and grew up in the woods in New England. After graduating highschool I moved to San Diego to apprentice with a Japanese aikido master there. In the early nineties I moved northwards to Santa Barbara where the local community college had a glass blowing program.
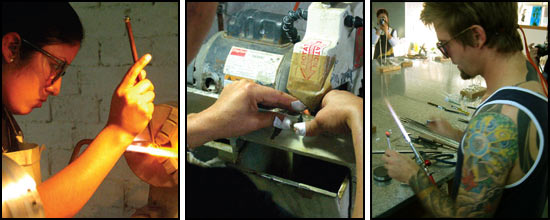
When we met at BMEfest in La Paz, Mexico, I noticed you have some great tattoos.
I got my first tattoo in San Diego when I was eighteen. I have no idea who the artist was — it is a triangular Nordic symbol on my shoulder. When I moved to Santa Barbara a big cholo named Curly did a few black and gray pieces. My favorite from Curly is a “gripping beast”, another Viking theme with an old school feel. After I started working at Pilchuck Glass School I would go to Seattle to get tattooed. I met Colin Delgado when he was working at Vyvyn Lazonga’s studio by the Pike Market. During my Pilchuck years he did all by big black pieces — solid black bands on my arms and legs and spirals on my back and legs. The idea was to make tattoos with designs big enough they could be seen from a distance. Tina Bafaro did my sleeve incorporating fallen autumn leaves and a big serpent on a Japanese inspired sea scape. More recently David Gilstrap did a cutting of a lotus motif on my stomach and legs.
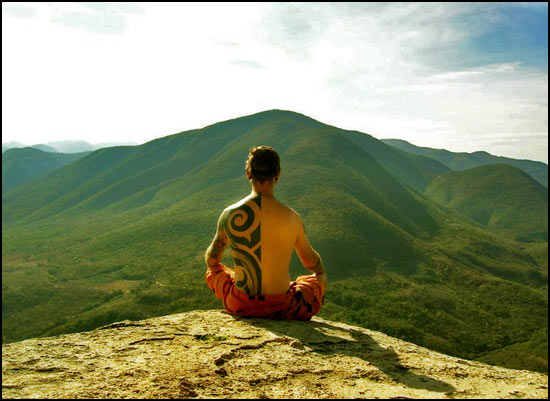
And you currently live in Oaxaca, Mexico, right?
Yeah.
How long have you been situated there and why did you relocate?
I moved to Oaxaca from Mexico City about three years ago. I had to escape the big city. I am not really a city person and twenty-three million is a lot of people in one place! Oaxaca is beautiful with mountains, beaches, pre-hispanic ruins, and a community full of painters and artists. Some friends pressure me to move back to the States, but honestly I don�t think I will ever go back there to live, there are too many places to explore on the planet.
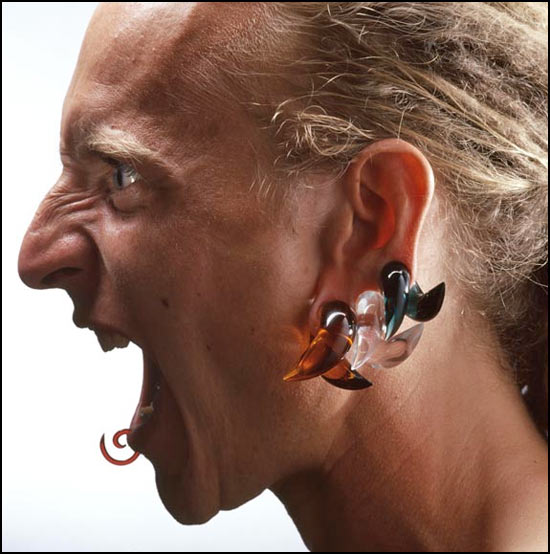
From the little news we get from the area it sounds like things are pretty tense. Does the political unrest there affect the day to day operation of Gorilla Glass?
We had a very rough time in Oaxaca in 2006. Before the national elections in Mexico there were six months when protestors took over downtown Oaxaca. Hundreds of barricades of burnt cars stopped traffic in and out of town, and all the government buildings were occupied. There were no police, thieves came in, and shop owners became vigilantes. My old glass studio was taken over by two busloads of armed men because of a private fight between the owners of the building. After three weeks of negotiations I managed to liberate all my equipment and moved the shop way out of town. Things have calmed down, and the military came in and restored order, if not peace and justice. Gorilla Glass has been a huge support in all this — because I am not dependant on tourism and the local economy, I can help in my small way by creating good employment. Poverty is the root problem.

When did Gorilla Glass come about?
My good friend Orfeo Quagliata invited me to set up a flame working production in Mexico City in 2002. Orfeo is an industrial designer from San Francisco and owner of Phuze, a glass design company based in Mexico City. I had a background of working with fashion designers in New York City, and he wanted to start producing and designing glass jewelry. I took advantage of being in Mexico to start my own line of piercing jewelry, and Gorilla Glass was born.
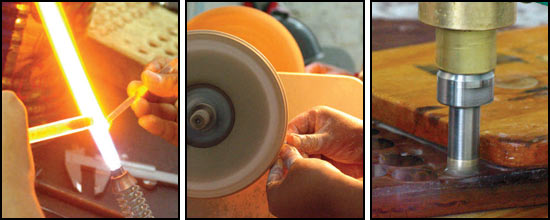
You just woke up one day and thought you would make some body jewelry?
Well no, I became frustrated making fashion jewelry! I would design two collections a year for Colette Malouf, and organized production. The glass became her specialty signature show pieces: lots of celebrities and glossy fashion magazines. Vogue even did a full page article on us working together. But the fashion scene is so pretentious and I wanted to be independent and make something for my peers. I started making piercing jewelry for friends in 1998.

What sort of training do you have?
I started glass blowing at Santa Barbara City College in 1992. They had a crude facility looking out on the beach. The teacher was usually drunk during class and we had total freedom to experiment and do what ever we wanted. I started flame working a couple years later (reheating glass rods on a torch). Bead maker Tom Boylin taught me how to work borosilicate glass, and I set up a small studio in my house. In 1994 I went to Pilchuck Glass School as a student. The following year I began working there as a technical coordinator for five consecutive summers. Pilchuck is where I recieved my serious education in glass. In the middle of a tree farm above Seattle, Pilchuck is the premier glass school in the world and they bring glass masters from all over the world to do intensive courses. Everyone works and lives together for three weeks with open studios twenty four hours a day. It is an extraordinary place.
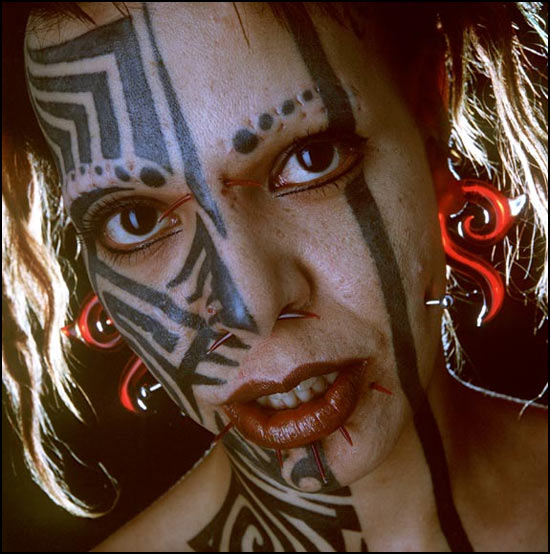
Who if anyone helped you on the way?
So many people have helped me it is impossible to mention them all, but here are some of the most important. Roger Parramore has been my biggest technical influence in glass. Karl Ittig and Lucio Bubacco showed me independently the possibilities of working soda lime glass on a torch. Michael Kramer continues to set an example of how to run a glass production shop. And Orfeo Quagliata brought me down to Mexico. His energy and enthusiasm for design is contagious.
What materials do you work with?
I work with two general glass types in production, soda lime and borosilicate. The glass I use depends on what color I want. There is a wider selection of transparent colors with the soda-lime glass, but is limited in scale up to half an inch. Borosilicate glass is available in larger sizes but with no color, or with a color accent or “sandwich” like the borosilicate plugs. It is much easier to work the borosilicate glass on a torch because of its greater resistance to thermal shock. The soda lime glass requires more sensitivity to work, and greater care in annealing properly. It is a complete myth that you can�t autoclave soda lime glass. Both borosilicate and soda-lime glass are non-porous, easy to clean, and odorless, which are all excellent characteristics for piercing jewelry.

What materials won't you work with and why?
I don�t work with any coatings on glass like fire on gold or enamels, fumed gold or silver, or external dichroic coatings, because they scratch or rub off. I don�t use lead crystal, which consists of thirty percent lead. Some studies have shown that alcohol can accelerate leaching of the lead. While we don�t store alcohol in piercing jewelry, it's better to be on the safe side. I stay away from cheap recycled bottle glass. For some special projects I use barium crystal. Barium crystal is a lead-free crystal with a high refractive index. It is the exact same glass they use to manufacture the top of the line, three hundred dollar a bottle Padron Tequila. If it is safe to store and drink tequila out of, it is safe to wear in your ears in healed piercings.
There has been some discussion about glass colorants in the piercing community. Colorants generally consist of less than one percent of the glass make up, and are bound to structure of the glass matrix. You can imagine glass colorants like a drop of food dye in a glass of water. Leaching does occur but very, very slowly and in miniscule amounts. The main danger with leaching is to the environment from glass dumped in landfills with colorants seeping into the ground water over fifty or a hundred years. There are warnings that leaching can be accelerated under special circumstances, in particular digestive juices accelerate leaching. So don�t eat the glass! But seriously, I have never seen a reaction to glass colorants leaching out of piercing jewelry.
A much more immediate risk with glass is breakage. Jewelry should be kept clean and regularly inspected for nicks and scratches. Always take the glass out before showering or going to bed and don�t wear glass while playing contact sports or slam dancing.
Give us a run down on the steps you take from the raw material to the finished piece.
I use many different techniques to offer the widest range of styles and colors possible. It would take a small book to describe all the techniques, which include fusing, blowing, flame-working, drilling, grinding, and polishing. The hand made element is what makes glass so special. Glass making is a skill and an art form — it is not injected molded or machined jewelry.
To give a brief example I will describe making a glass claw. First the glass batch is melted in a large furnace. Next a team of glass blowers gather the glass onto metal “puntils” and draw them into long glass rods, which are annealed in special ovens to remove thermal stress. When the glass rods are cool they can be handled and re-heated on a torch where they are flame sculpted into their rough shape. The claw is annealed again. The next day the head of the claw is ground and polished on a series of diamond wheels. Finally they are washed and examined for flaws in quality control. Sizing and packaging is last. Most jewelry passes through at least three teams of glass workers depending on the process.
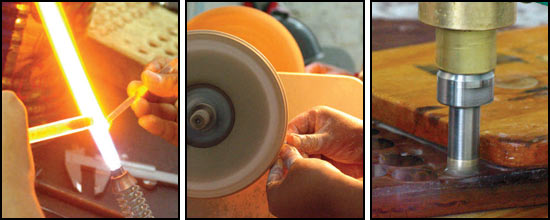
What are your favorite things to make?
My favorite thing is working on new design prototypes or making custom jewelry for my friends. I have made jewelry for people to wear in weddings, which is cool too.
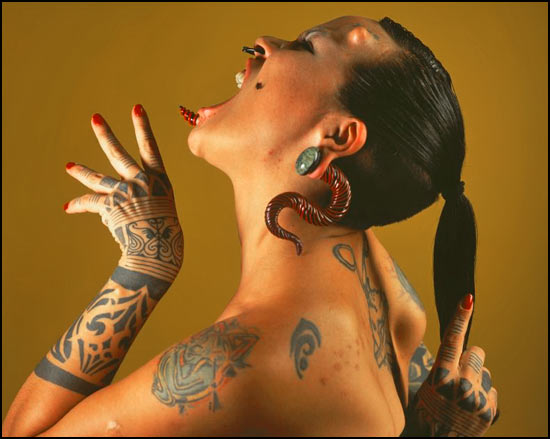
Anything new up your sleeve that we can expect in the near future?
I have four new color combinations I am about to release in the Power Plugs, really bizarre and unique color effects. Also I am working on a line of large glass plugs up to two inches. Another project I am really excited about is kiln-casting, a whole new process I am exploring which should open up some completely different design possibilities. Keep looking out!
Finally, do you notice any sort of difference in reactions you receive from people in the US compared to Mexico? Even beyond the general population, how about your employees at Gorilla and other business people you deal with? In my experience its double-edged — a benefit in some cases and an hinderence in others.
Well, Mexico is much more class-oriented than the United States. I will never be upper class in Mexico and that is fine with me. Reactions to the tattoos vary a lot, but mainly on generational lines, the same as the USA. Young people love them, and the older people are more critical as a rule. As a foreigner I am given more leeway to be different. Luckily I am my own boss — job discrimination is still wide-spread down here. At work it always takes new employees a little time to get used to me. Almost all my employees are women from traditional families from small pueblos. I am definitely a little strange and exotic to them, but working together day to day you develop a connection and mutual respect. My people are fantastic, really hard working and proud of the quality of what they do.
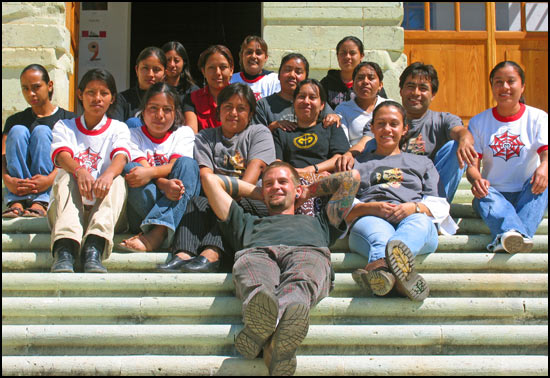
Click here to comment on or discuss this article.
Copyright © 2007 Ryan Warden and BMEshop.com. This online presentation copyright © 2007 Shannon Larratt and BMEzine.com. Requests to republish must be confirmed in writing. For bibliographical purposes this article was first published online April 23rd, 2007 by BMEZINE.COM in Toronto, Canada.
All Guest Columns | Return to BME/News
|